This architecturally designed home is located along the eastern coast of the Whangaparaoa Peninsula, with magnificent views across Stanmore Bay.
The home was built in 2009 and the Cedar had not received any maintenance before the customer contacted us.
Cedar located along exposed coastlines has different requirements than Cedar in tree covered areas. Without any shelter, the Cedar is fully exposed to the harsh New Zealand sun, which can burn the timber fibres on the exposed faces and dry out the boards.
Coastal winds can also be strong and contain higher amounts of organic matter, such as dust, pollen and sea salt.
Due to the lack of maintenance and exposure to the elements, this Cedar home required a complete restoration.
Maintenance Timeline
The customer first approached us on the 25th of January, 2024.
- 1st February, 2024 – Initial onsite assessment completed.
- 8th February, 2024 – Quote sent.
- 26th March, 2024 – Team arrived onsite to start the job.
- 4th April, 2024 – Job completed.
Cedar Maintenance Process
Before oiling, the Cedar required a deep clean to remove all the built-up organic matter and burnt fibers on the surface of the timber.
The customer wanted a golden look for the Cedar. We used Wood-X penetrating oil in Kauri Gum, which is the most popular and natural Wood-X colour tone.
As the front of the house is the main feature area – and the faces most exposed to the sun – we allocated more time and materials here to make sure it looked stunning.
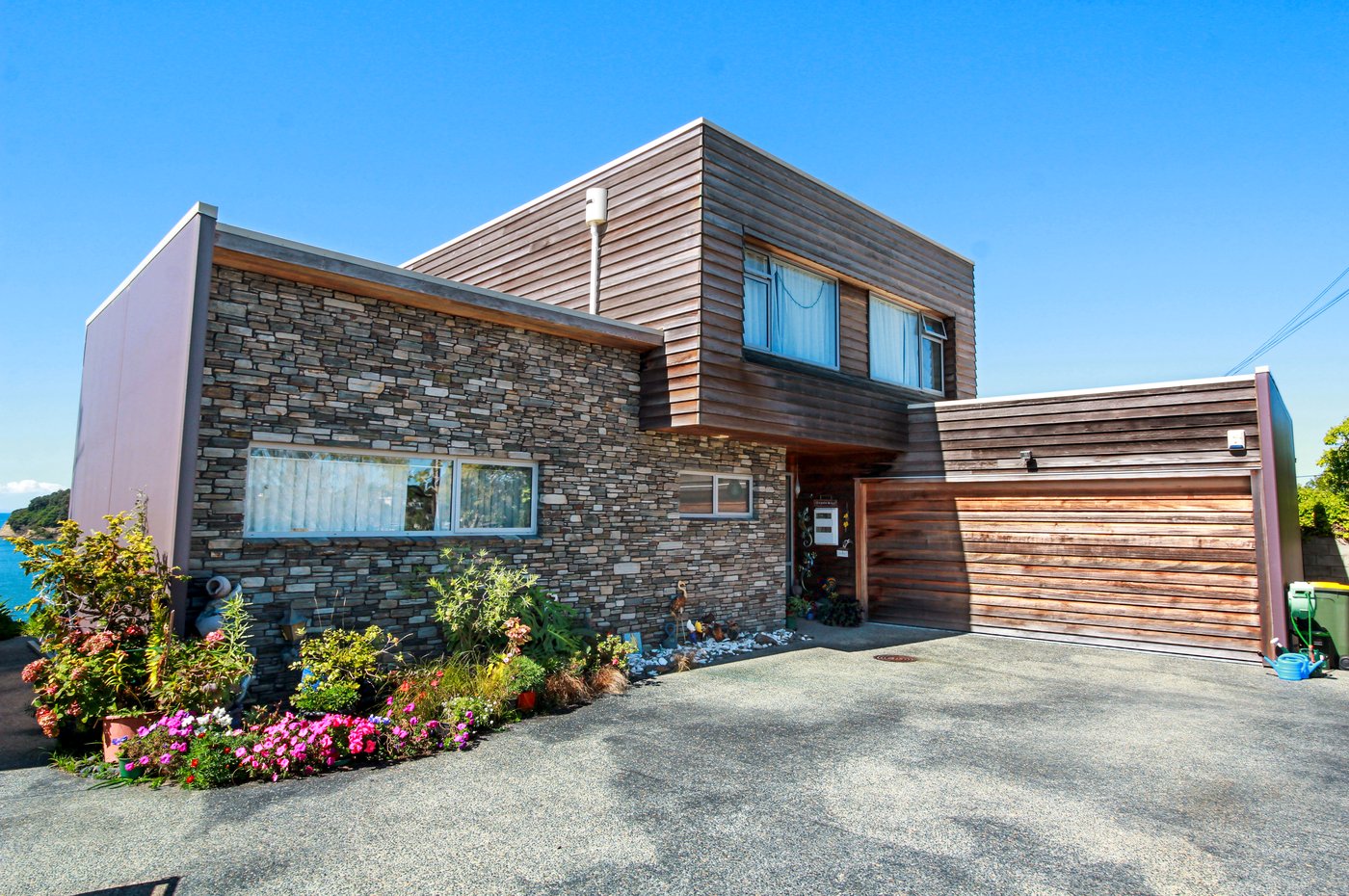
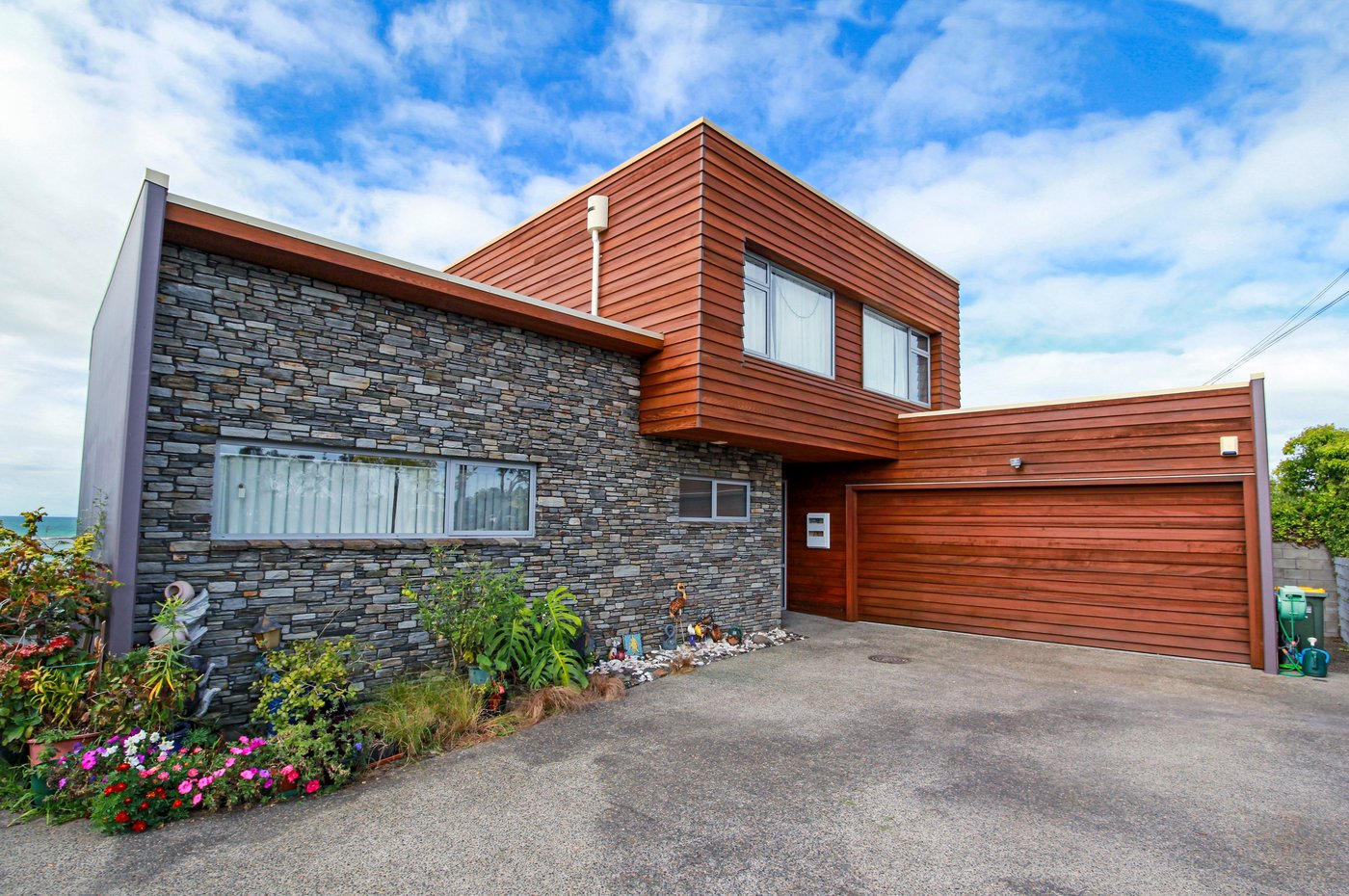
The colour of the garage door (in the before photos) shows what the boards would have looked like if they had been washed previously.
Unfortunately, the garage had been water blasted by someone unfamiliar with Cedar, leaving the surface streaky and damaged. Because the timber is so soft, these lines will stay in the timber forever, unless they are either washed or sanded out.
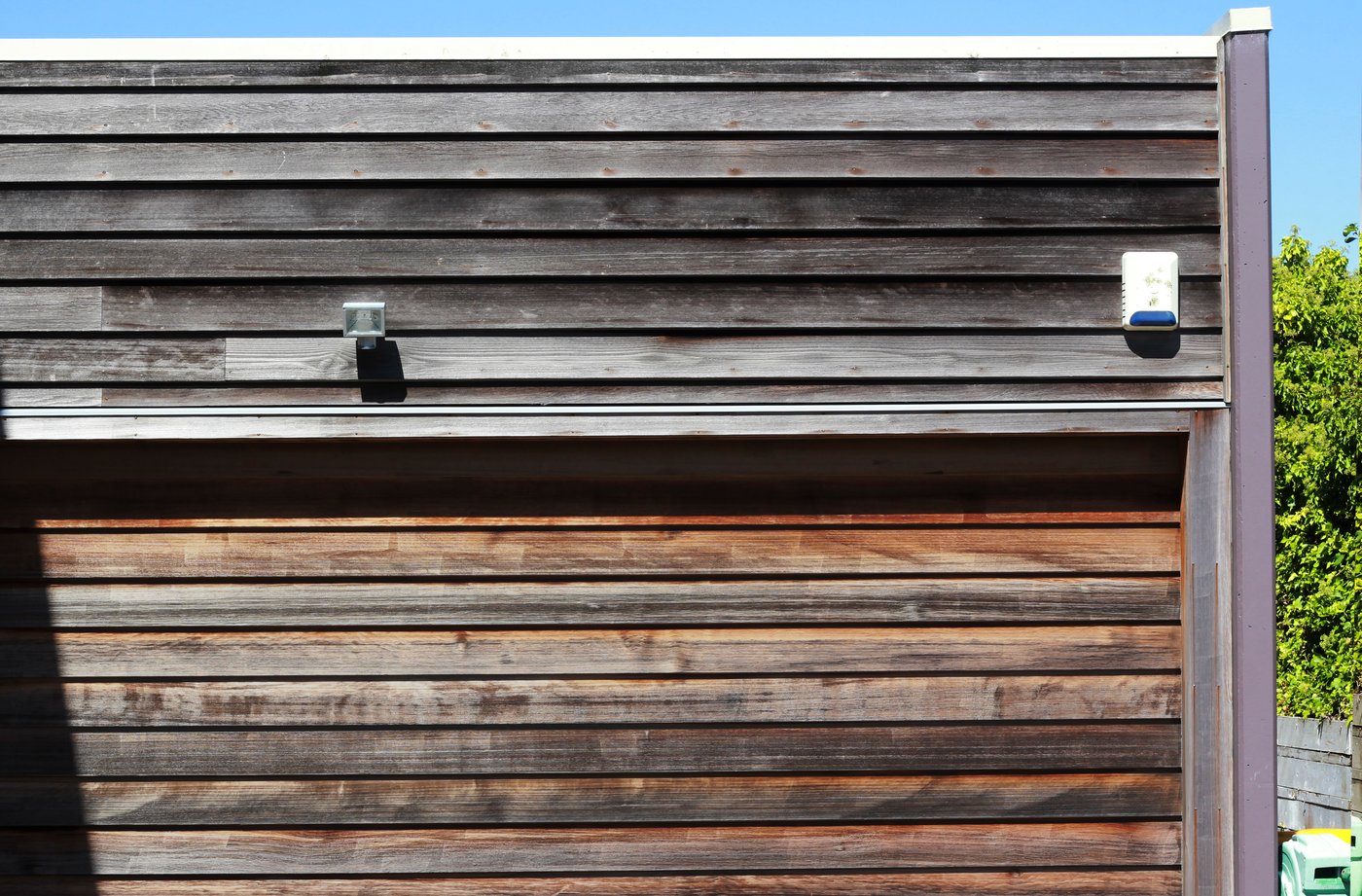
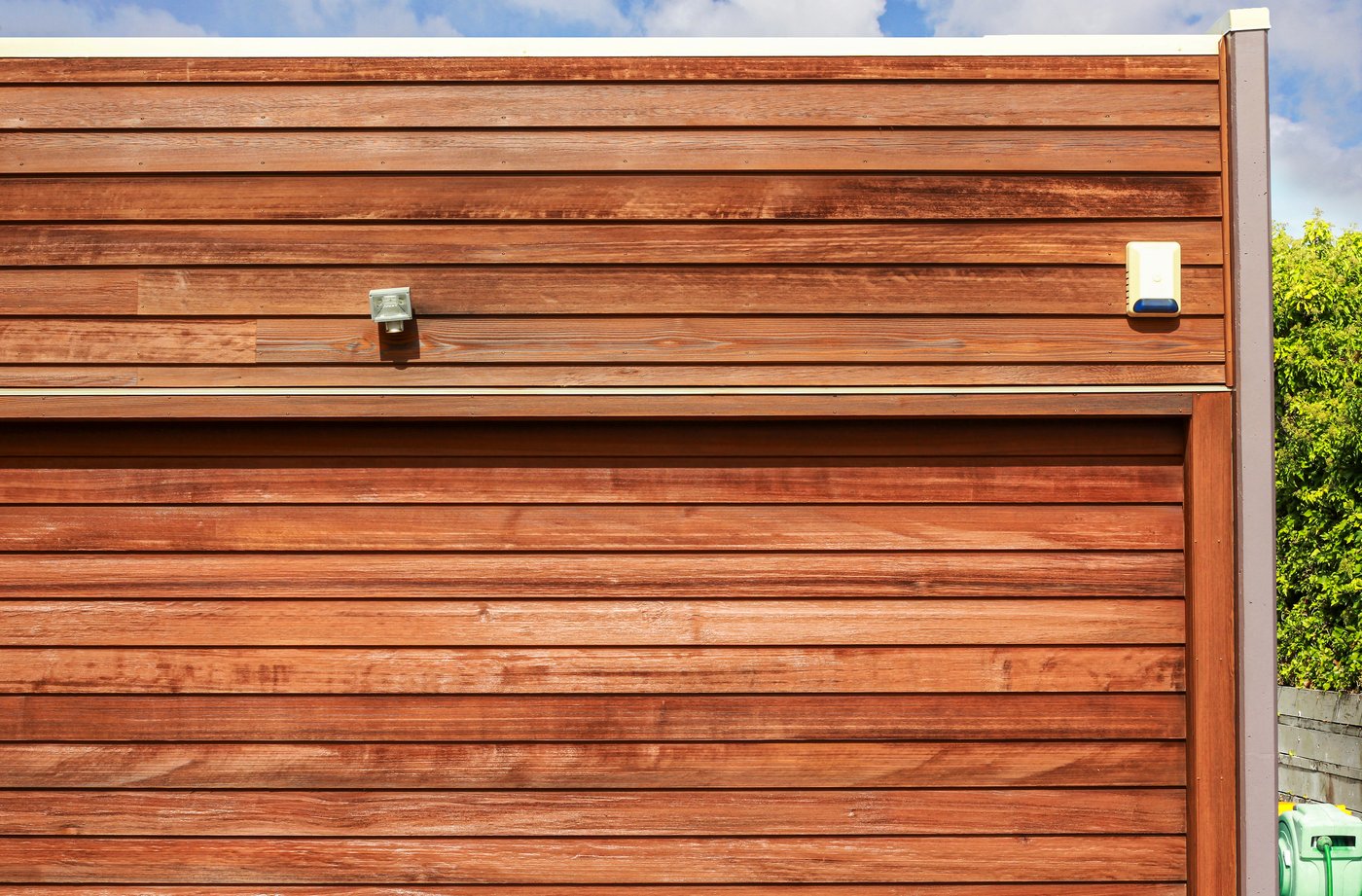
Above the garage door, the boards have been oxidised by the sun, giving them a burned and blackened appearance.
After putting drop cloths down, we sprayed oil from the bottom up, then across the boards, and by the time we got to the top corner, we had to start again as the oil had already been sucked into the timber.
This was coated 4 times in an hour, and the section above the garage door alone would have used 1.5 litres of oil.
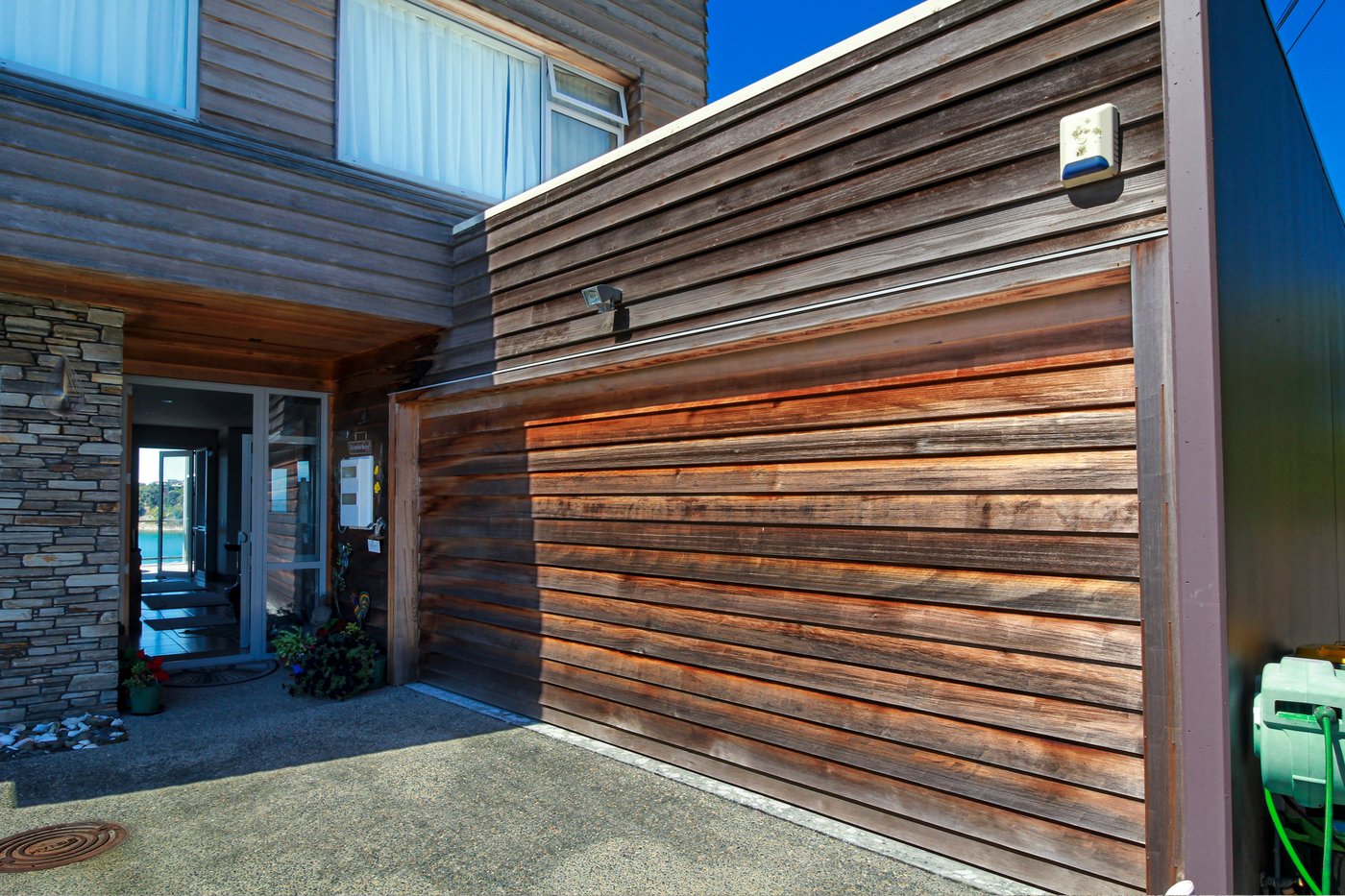
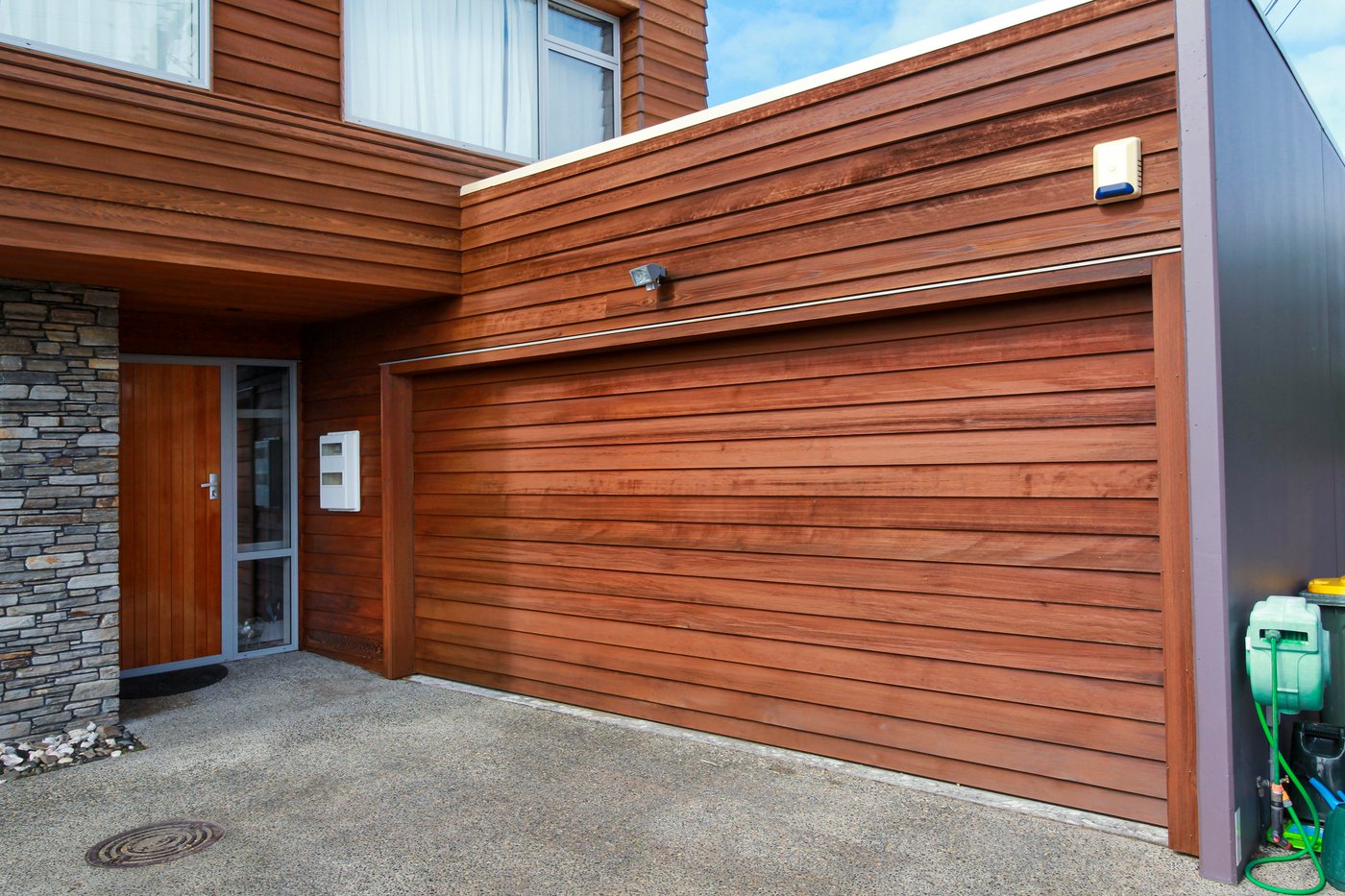
We then left it for 24 hours and came back the next day to apply another coat, mainly because it’s a feature area and we wanted it to pop, rather than still look thirsty.
On the face running perpendicular to the garage door, the boards have been bleached by the sun. Walls facing to the west can sometimes get just as warm and weathered as the northern faces, especially if there is no tree cover.
We recommend that sun-exposed areas are recoated every 2-3 summers. As these boards were so dry, we will return in 9-12 months for a recoat.
This gives the oil a chance to really suck into the pores of the timber before adding more. If done any sooner, the oil will sit on the surface and wash off when the rain hits.
Cedar Maintenance Challenges
The biggest upfront challenge for this job was how steep the property is at the back. As shown in the photos below, the house is built on a very steep coastal hill and required extensive scaffolding.
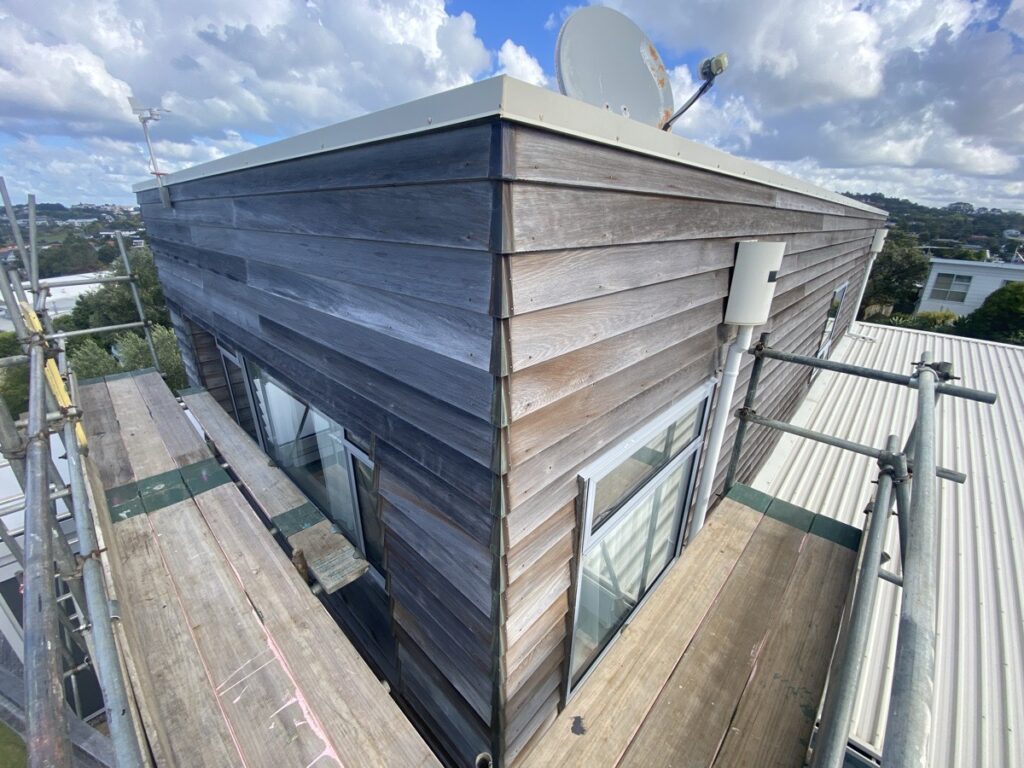
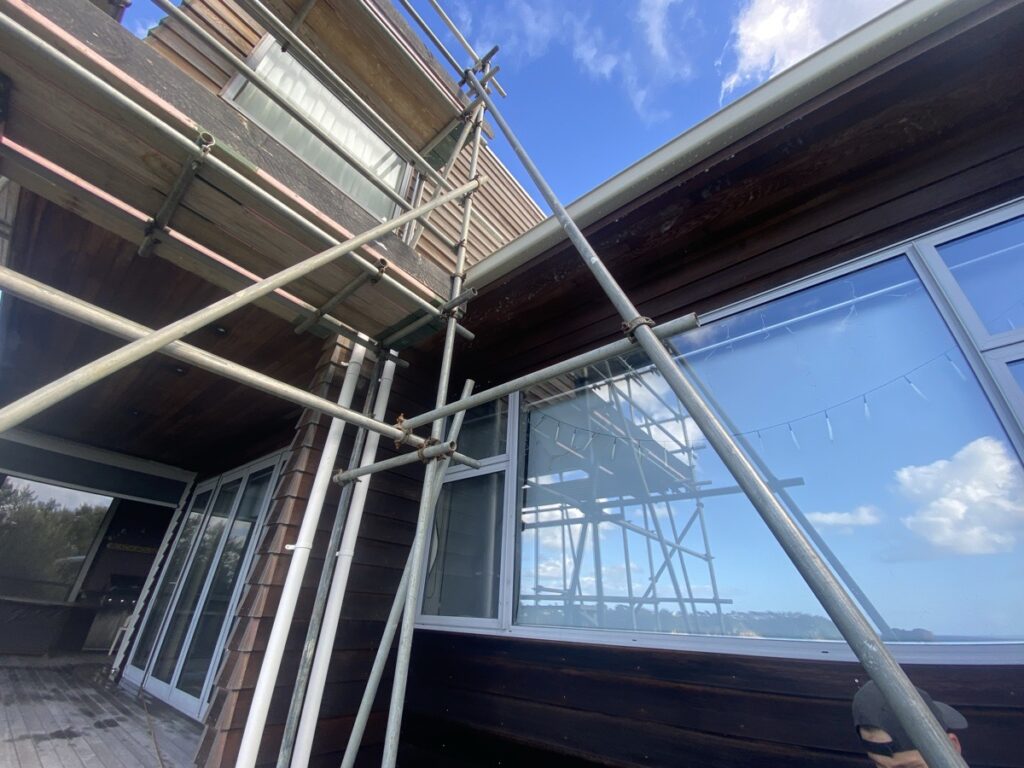
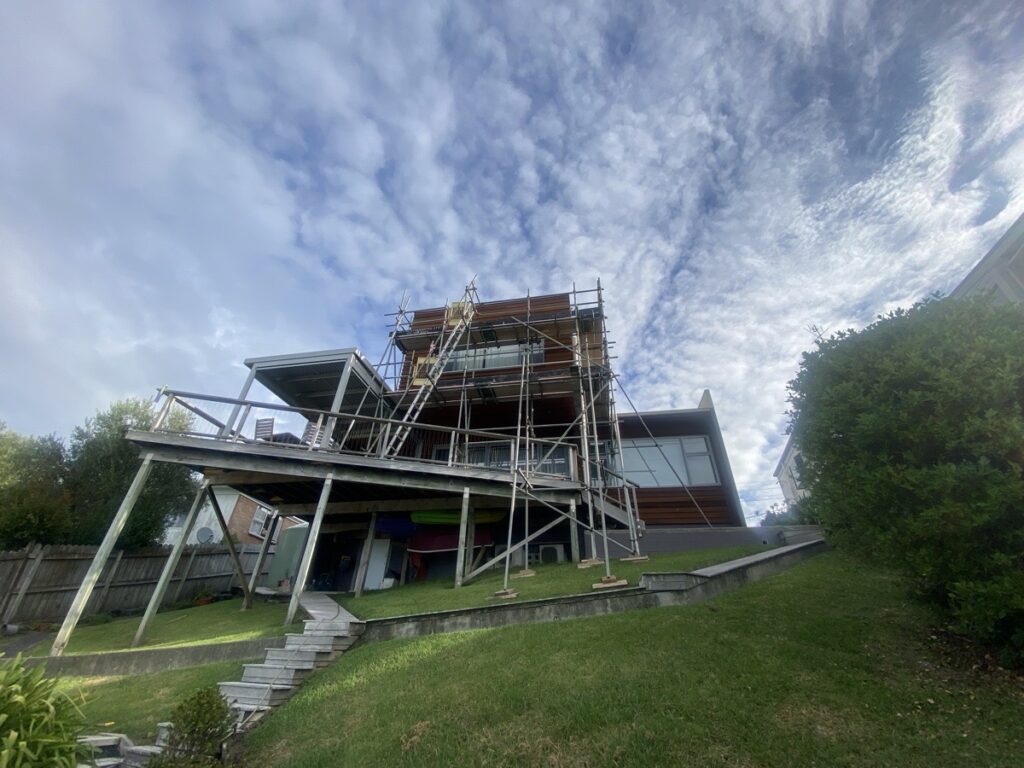
The next big challenge was just how dry the Cedar was.
The boards used for many Cedar homes are scalloped at the bottom, so that they overlap the board below and sit flush. The boards on this home are solid timber without any decorative features, allowing the boards to sit on top of one another.
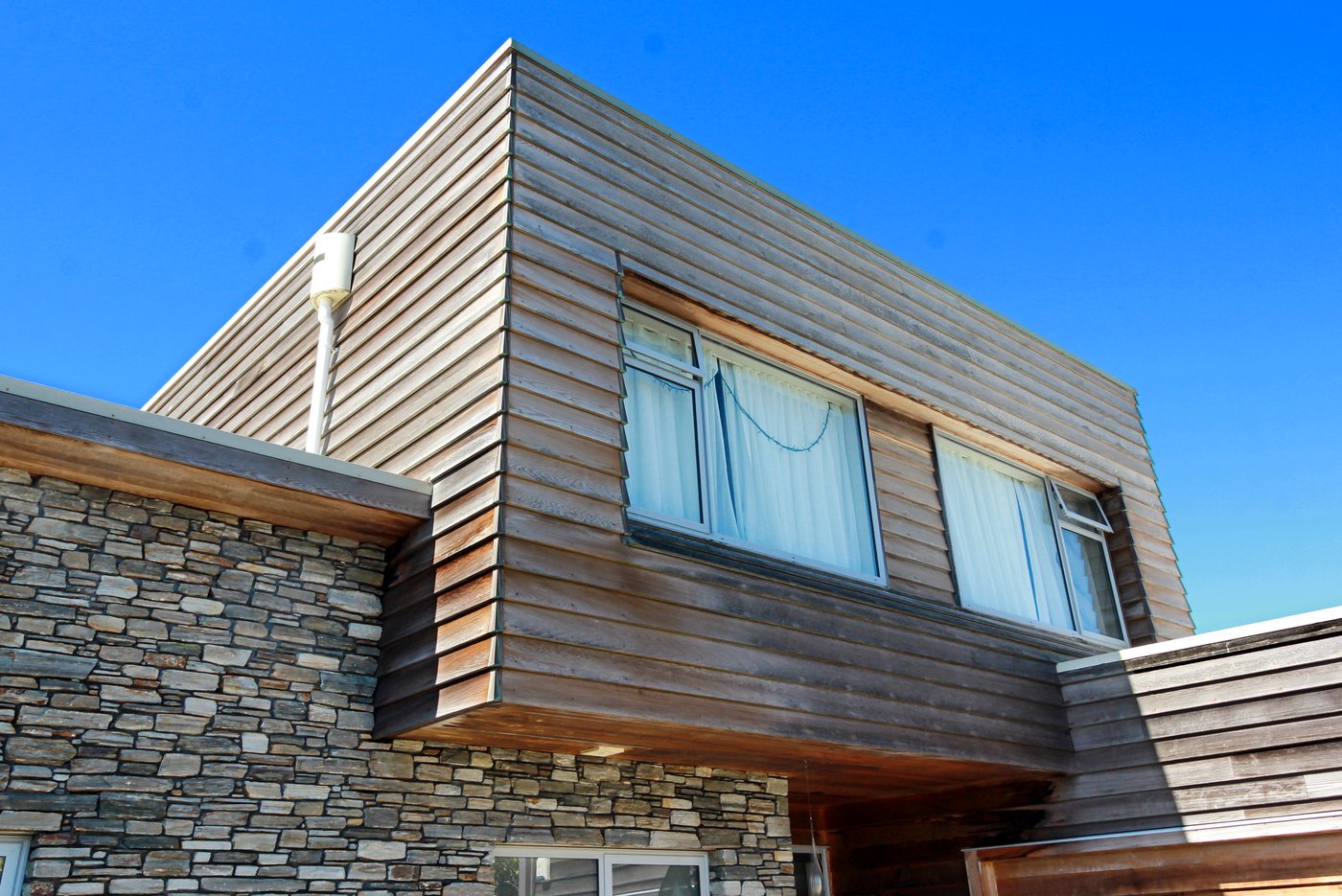
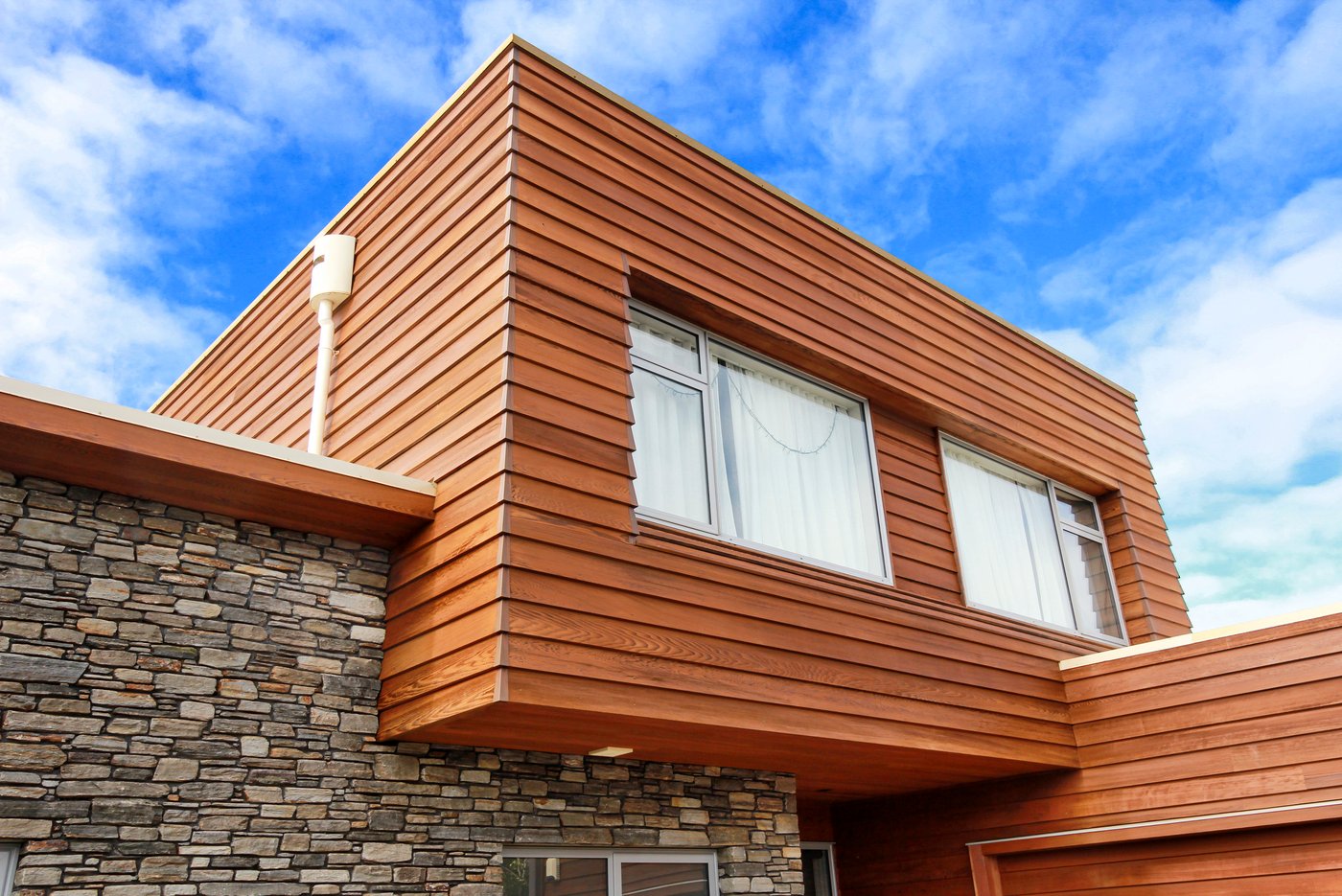
They are not much thicker than standard boards, but the difference is that the thickness goes all the way down. This thickness makes the boards very durable, as the thinnest part of the board is where most of the cupping occurs.
The thickness of the boards, along with how dry they were, required more coats of oil than usual and anyone untrained in Cedar maintenance might have slapped on a coat of oil and called it a day. The end result would not have been pleasant to look at.
Ongoing Maintenance Requirements
We recommend recoating sun-exposed faces every 2-3 summers. That doesn’t mean the whole house, just the faces exposed to the harsh UV. The rest of the house may not need further maintenance for 5-7 years.
The Final Outcome
The restored Cedar makes it look like a brand-new house. Contrasted with the grey schist, the lovely golden hue creates a timeless alpine look, both homely and sophisticated.
The owner was away while we did the maintenance and was stunned by how it looked upon their return. They knew we would make it look better, but they didn’t think the transformation would be so dramatic.
Even Mark was impressed with how well the Cedar polished up, and that saying a lot having been in the business for 30 years! What a fantastic result for the homeowner, and a restoration we are very proud of.